July 29th 2023Precision Benchrest shooters and F-Class shooters prefer premium brass from Lapua or Norma. (Lake City makes quality brass for military calibers. Premium brass is more accurate, has more consistent velocity, and lasts longer. Many shooters know the importance of brass, but few of us are aware of how cartridge cases are made. Here’s a look at how it’s made. Top Deep-Draw RAM Illustration from Demsey Mfg.The first step is to stamp a brass disc from metal strips. The brass is then extruded into a cylindrical form through a series stages. The brass is pressed through a die at high pressure during the extrusion procedure. Typically, this is repeated two to three times. In the traditional “draw” method, the case is stretched in three to five stages using high-pressure rams that force the brass into a die. RWS, which produces some of the most uniformly-sized brass in the industry, still uses the traditional draw process. “It begins with cup drawing, after the bands have already been punched out. RWS cases are drawn three times and are then annealed and pickled and rinsed. They are also subjected to quality improvement measures after each stage. This results in a specific hardening and increase of the brass cases’ resistance to extreme stresses.” FYI, Lapua uses the traditional draw process for the majority of its cartridge brass. (Lapua does use some proprietary steps which are different from RWS methods.) After the cases have been extruded or drew to maximum length, they are trimmed, and the neck/shoulder is formed. The extractor groove is then formed or machinized on rimless cases, and the primer is placed in the base. A “bunter” is a hardened steel plug that can be used to form the primer pockets. The photos below show the stages of forming a cannon case (20mm) (courtesy OldAmmo.com), as well as bunters used to form Lake City rifle brass. This shows the draw process, as opposed to extrusion. The process for drawing-forming rifle brass is the same as that of this 20mm shell. It is just done on a smaller scale. The head of the draw at this stage is slightly rounded and there is no provision for a primer. The final drawn cases will be trimmed and then run through the head bunter. A punch ground to the intended contours of the inside of the cases pushes the drawn into a cylindrical case and holds it in position while another punch rams the case from the opposite end, slamming the bottom flat. This secondary ram is used to hold the headstamp-bunter punch. The headstamp punch bunter has a protrusion at the end for the primer pocket and raised lettering all around the face of the tool to form the stamp writing. It is obvious that this is a mirror-image of the case head. Small cases such as the 5.56×45 can be headed in one strike. For larger cases, such as 7.62×51 or 50 BMG, you will need to strike the case once to create the primer pocket. Then, you will need to strike the case a second time to finish the pocket and flatten the head and imprint the writing. This second strike hardens the brass so that it can withstand the pressure of firing. “Thanks to Guy Hildebrand of the Cartridge Collectors’ Exchange at OldAmmo.com for providing this photo of a 20mm Draw Set. Bunter photo by River Valley Ordnance.Similar Posts:Tags: Brass Production, Cartridge Brass, Deep Draw, Deep-Draw Ram, Draw Process, Lapua, OldAmmo.com, RWS
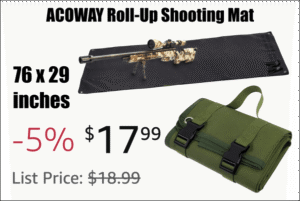
Discounts of the Week on DealFinder 509: AccurateShooter
At the request of our readers, we offer a few” Talks of the Week” on June 23rd, 2025BargainFinder 509: AccurateShooter’s Deals of the Week. Our Best Deal choices are available